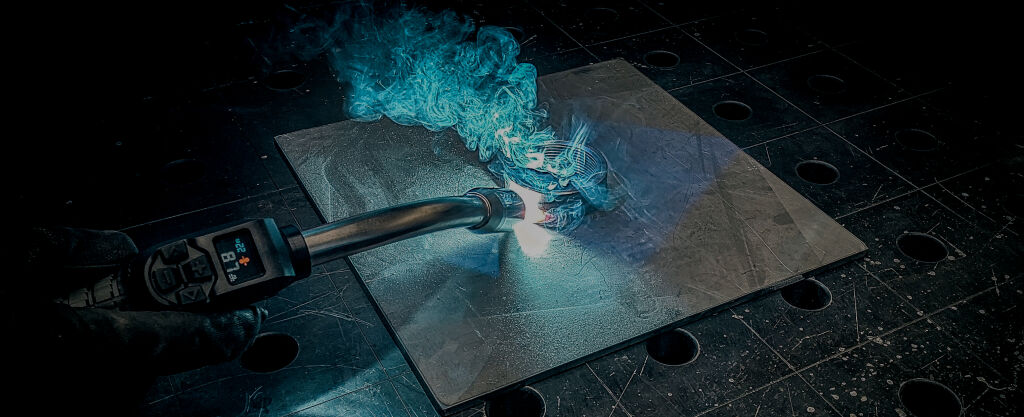
Tubificio Lombardo S.r.l.
Le rendement et la fiabilité des pipelines bien soudés
Tubes en acier et tuyaux soudés avec la torche de soudage Flexlite GXe
Entreprise
Tubificio Lombardo S.r.l.
Site web
tubilomb.itIndustrie
Structures métalliques pour le bâtiment
Emplacement
Lombardia, Italy
Matériau de base
Fe
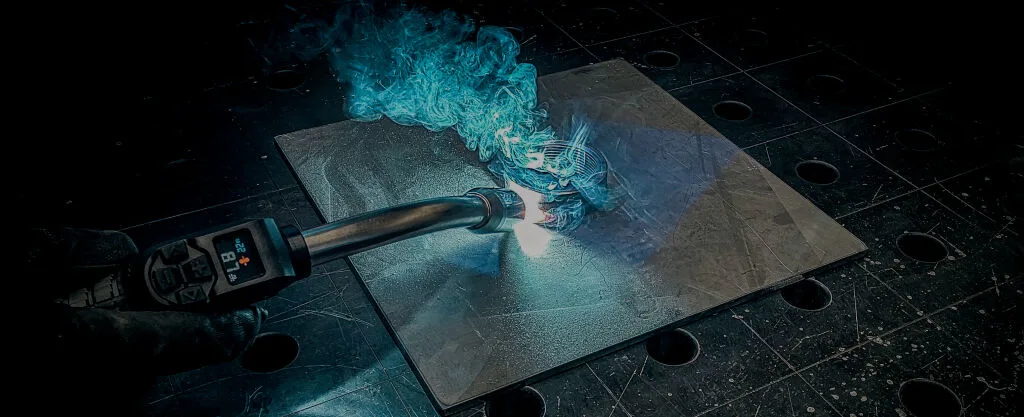
La torche Flexlite GXe a facilement maîtrisé les cas d'utilisation à ampérage élevé et constant chez Tubificio Lombardo.
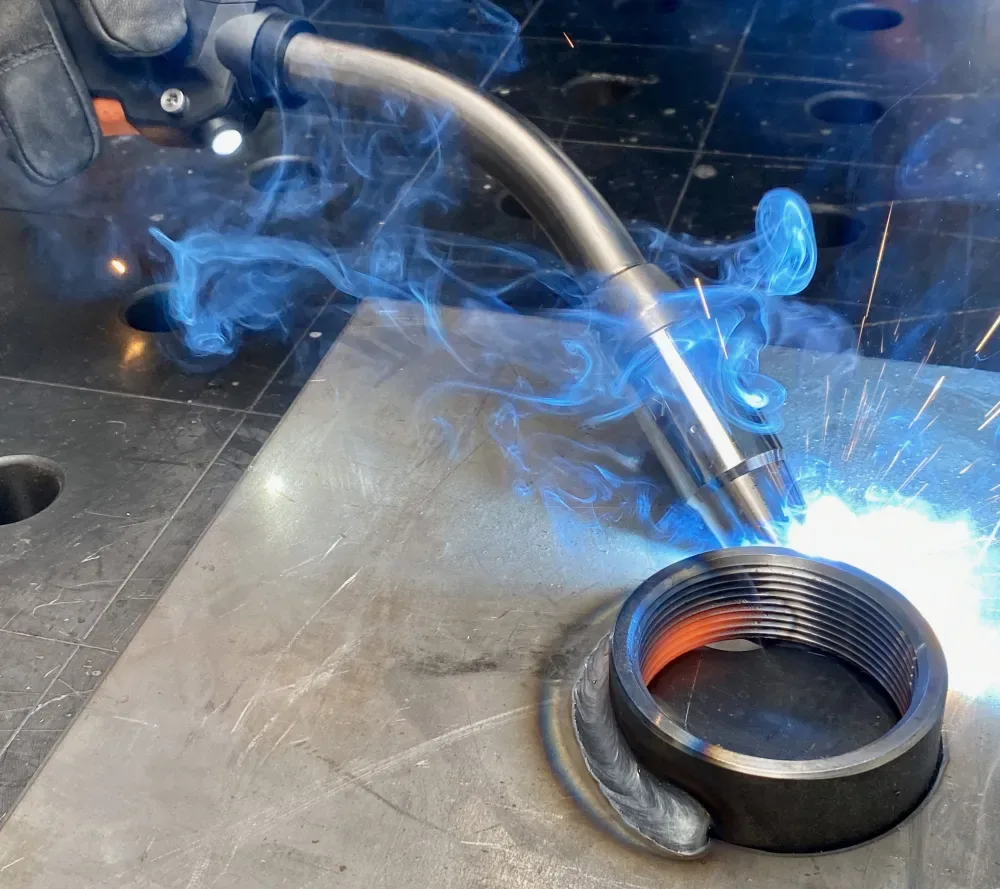
La torche de soudage Flexlite GXe est dotée de fonctions de refroidissement améliorées.
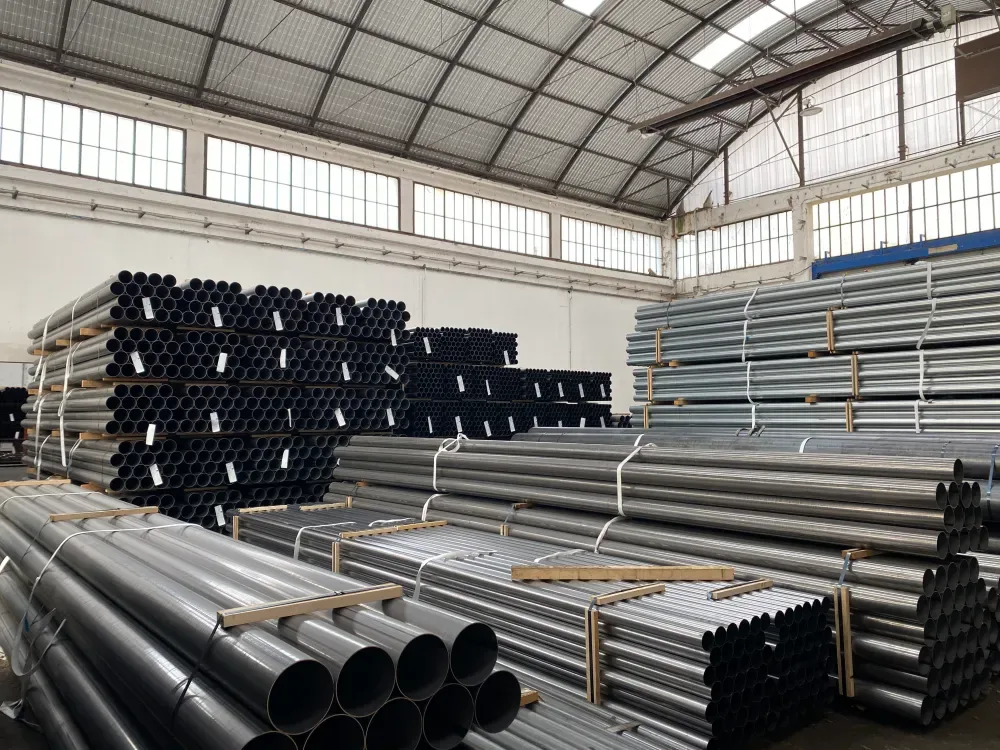
Tubificio Lombardo soude des tubes et des tuyaux.
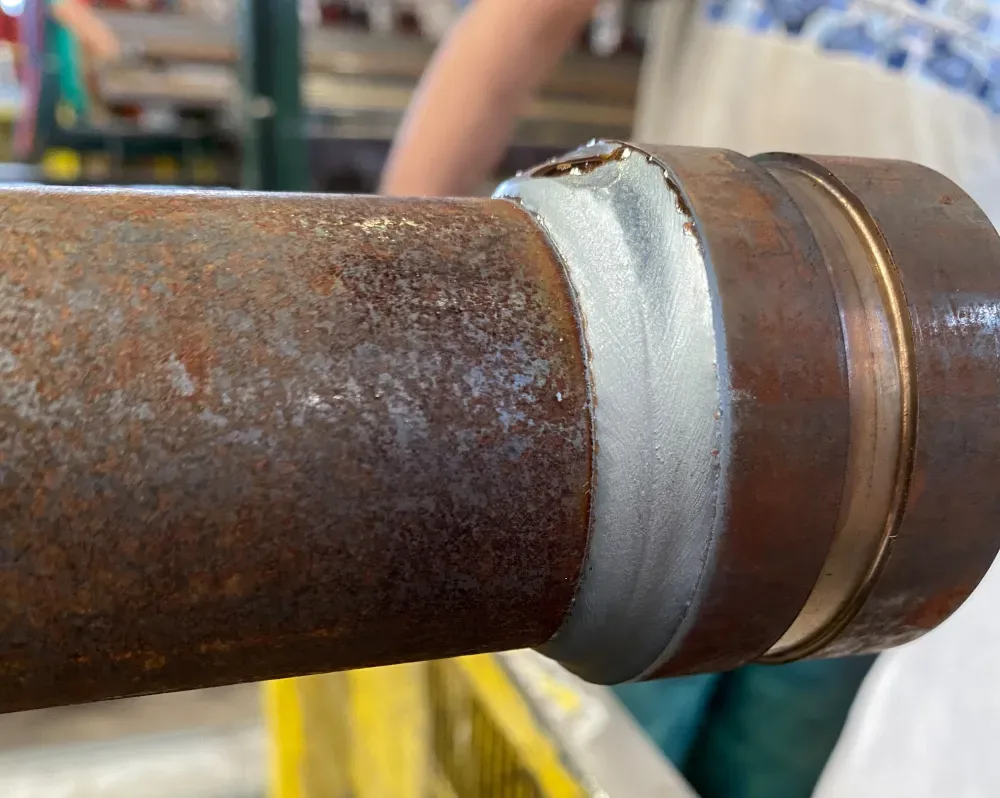
Tubificio Lombardo a piloté la torche Flexlite GXe MIG/MAG pendant deux semaines.
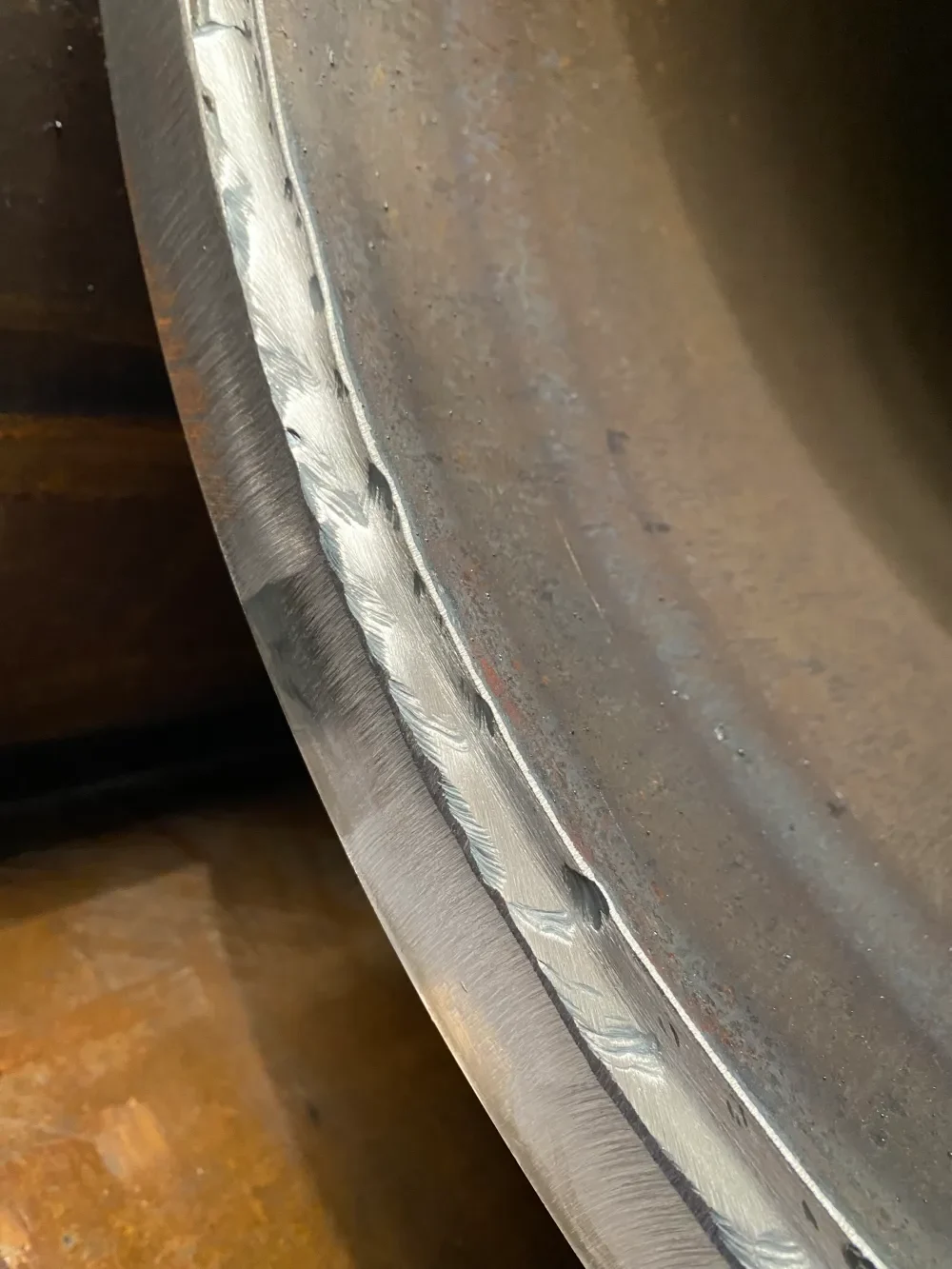
Exemple de pièce soudée avec la torche Flexlite GXe.
Parcourir notre offre
Famille de produits
La Série de torches MIG/MAG Flexlite GXe est conçue pour répondre aux exigences des soudeurs professionnels qui ont besoin de fiabilité, de précision et de durabilité dans chaque soudure. Conçue pour les tâches de soudage exigeantes, la Flexlite GXe offre une excellente commande, précision et confort, jour après jour, soudure après soudure.