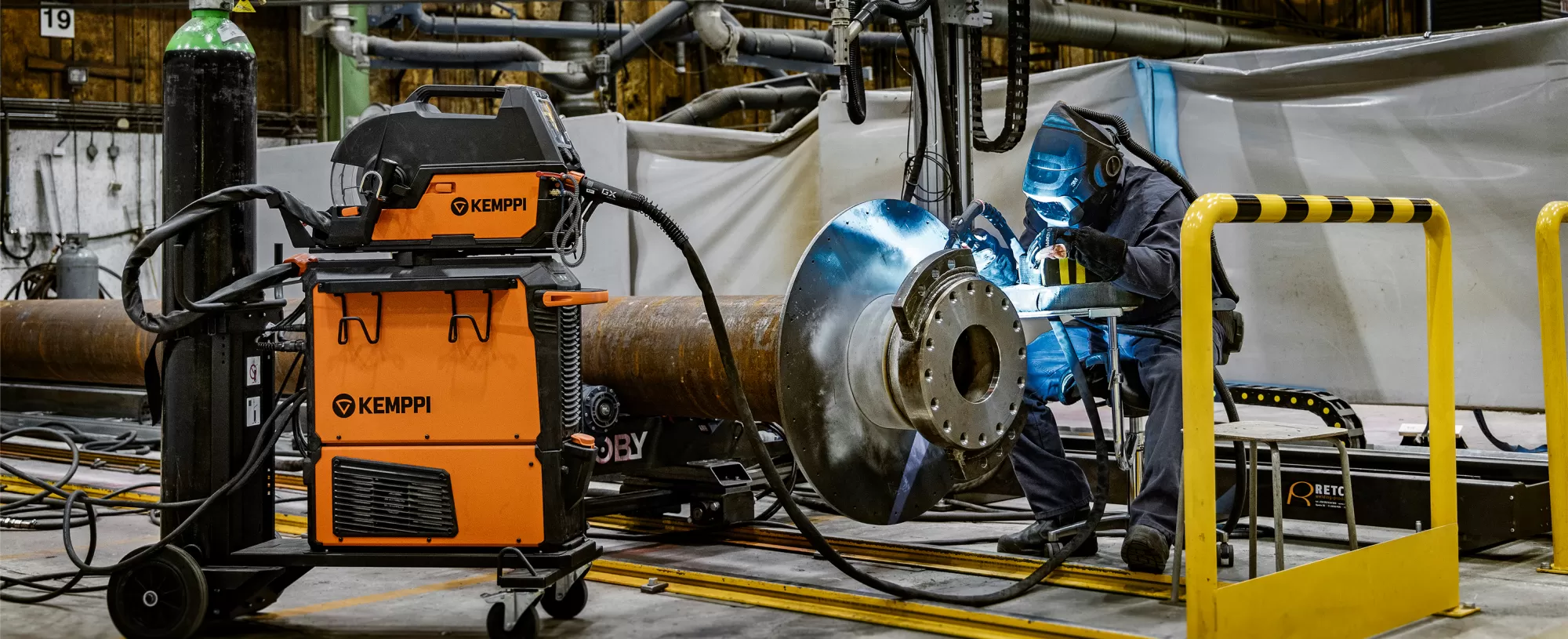
Turula Engineering
Top-class industrial equipment manufacturing
X5 FastMig Pulse meets even the most challenging welding needs
Company
Turula Engineering
Website
turula.fiIndustry
Machine manufacturing
Location
Outokumpu, Finland
Base material
Special materials, Ss
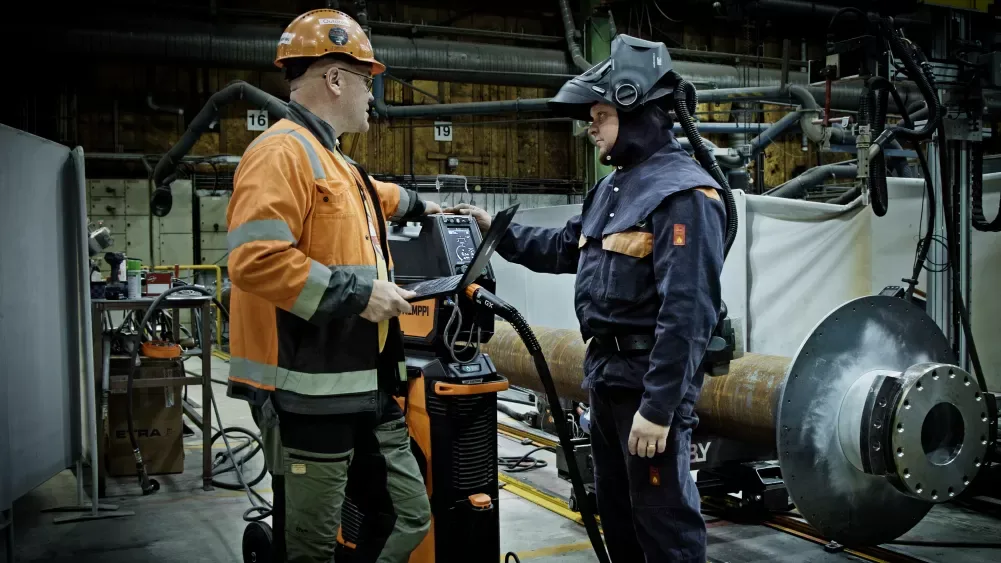
Welding Manager Antti Nykänen and Welder Timo Voutilainen setting up the X5 FastMig Pulse.
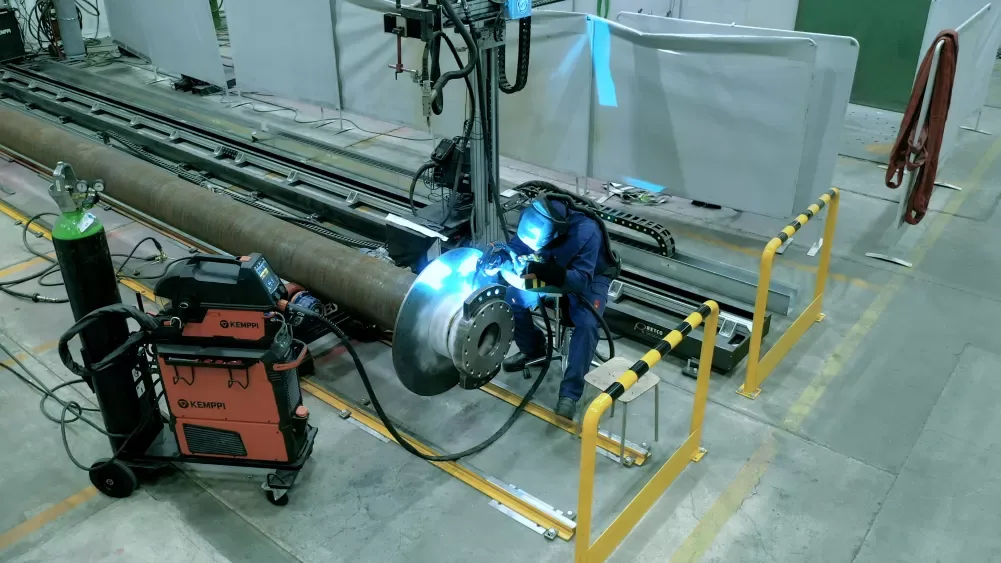
X5 FastMig's soft and spatter-free arc as well as the versatile welding properties are appreciated.
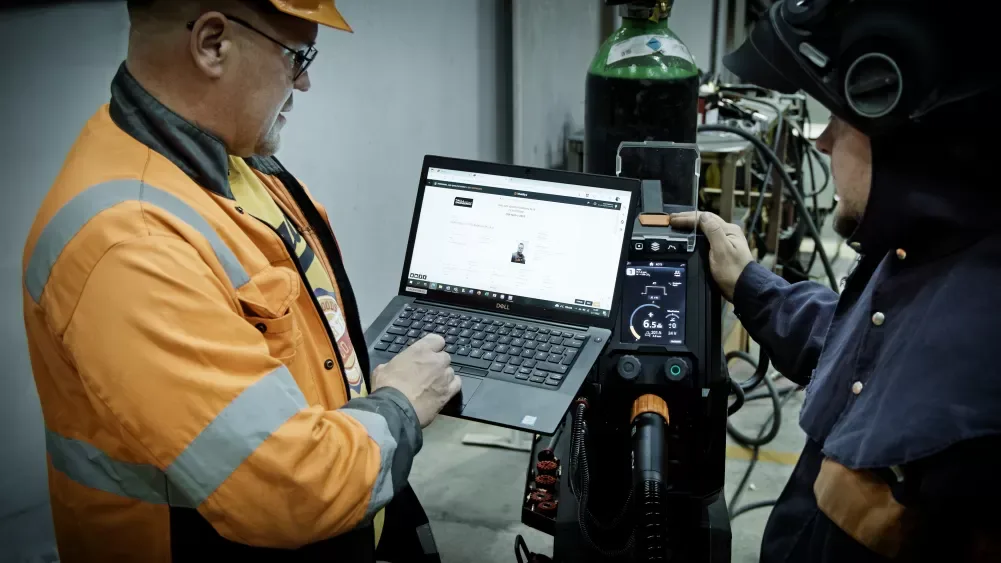
Turula has used Kemppi's WeldEye solution for managing welding production since 2011. The new X5 FastMig APC Wire Feeder has integrated connectivity WeldEye software.
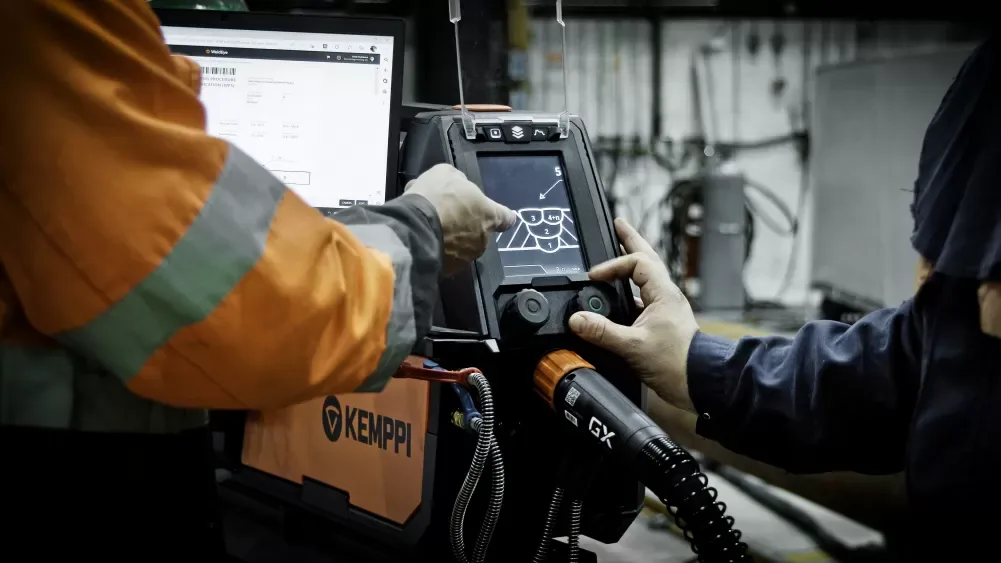
WeldEye's Digital WPS feature in action with X5 FastMig Pulse.
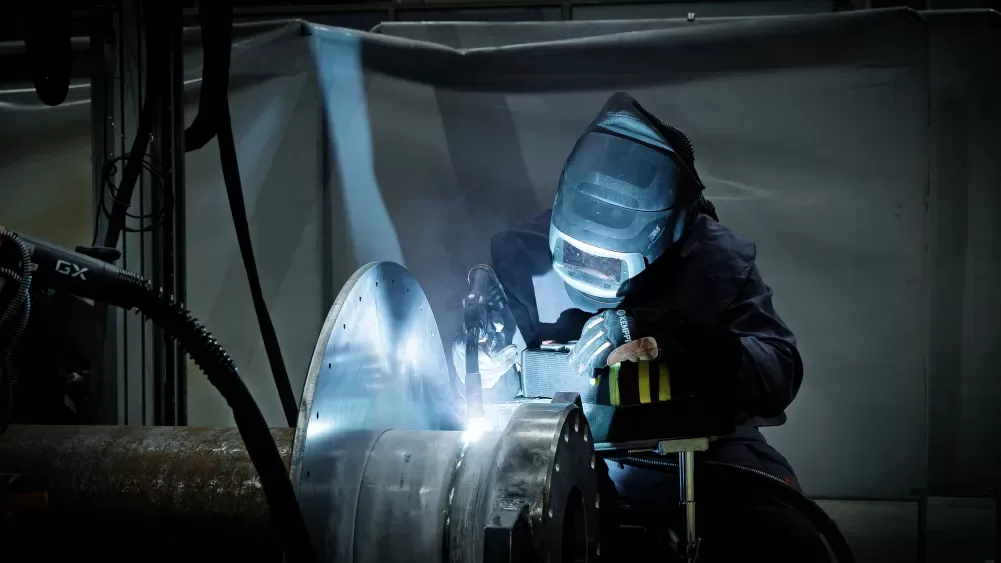
Turula Engineering is specialized in welding complex pieces of different shapes and sizes.
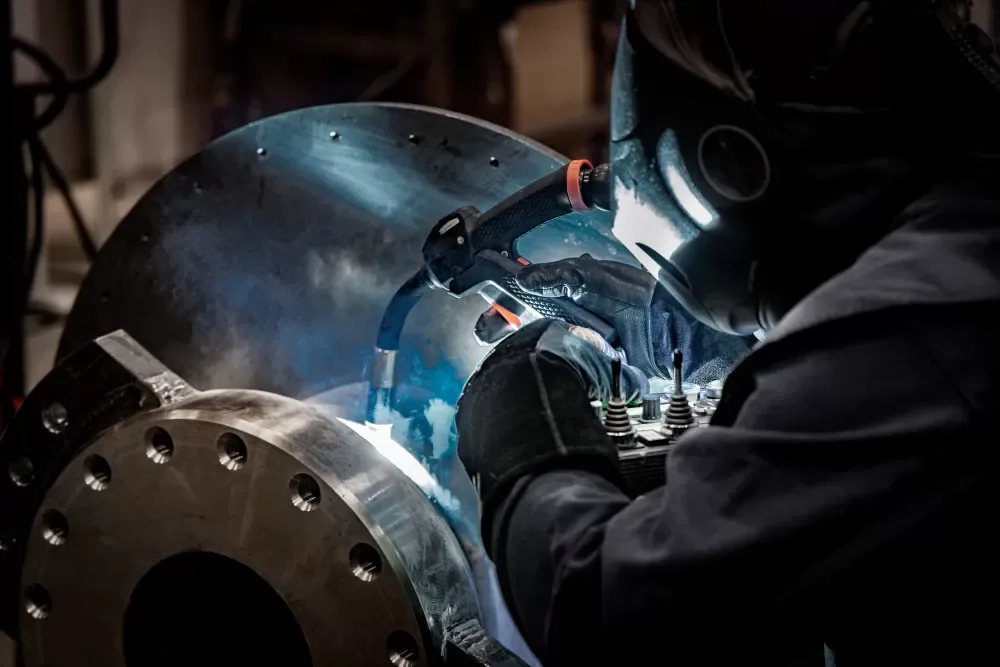
X5 FastMig Pulse is equipped with Flexlite GX MIG welding gun.
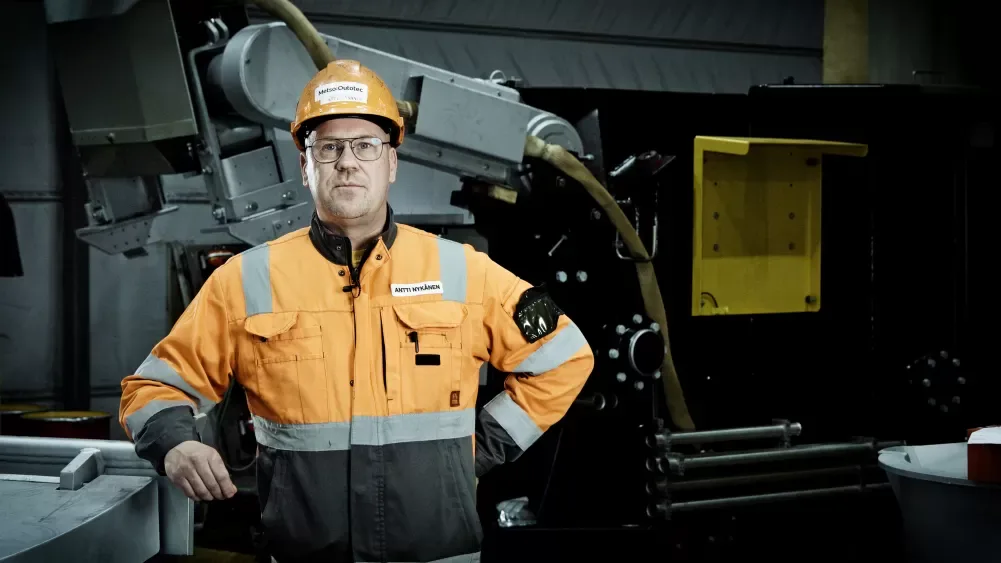
Antti Nykänen is happy with the the cooperation and versatile partnership with Kemppi.
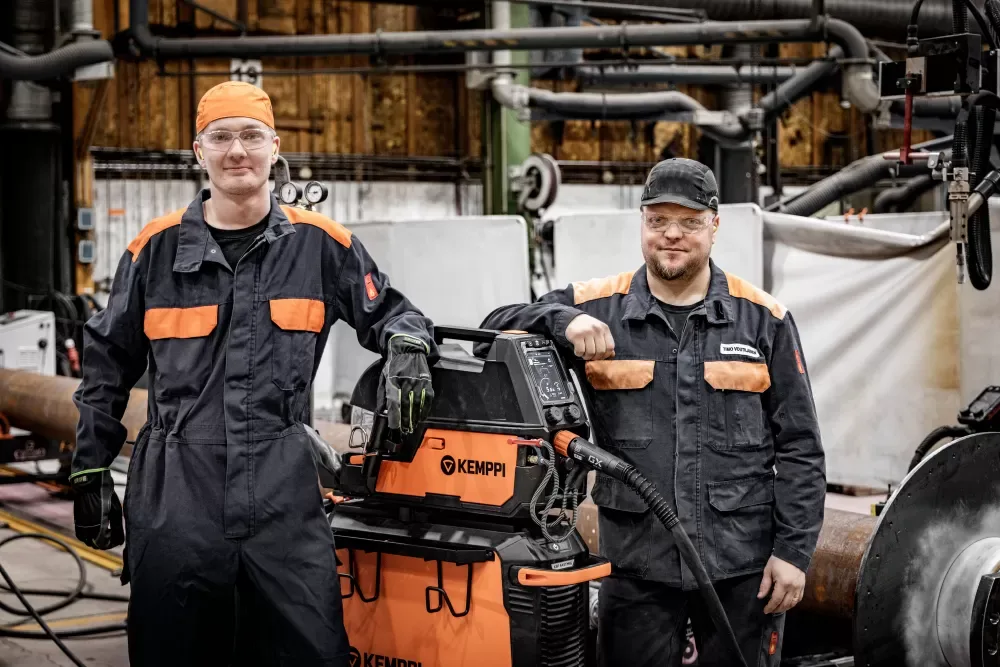
Welders Atte Nykänen and Timo Voutilainen from Turula Engineering.
Featured Solutions
Product family
360-degree modular multi-process welder primarily focuses on high-performance MIG/MAG welding. X5 FastMig offers setup options for manual, synergic, and pulse welding. A wide range of accessories brings flexibility and efficiency to welding production processes