
Meyer Turku
World-class shipbuilding with a long experience
The Master M 323 meets the needs of the shipyard industry banner
Company
Meyer Turku
Website
meyerturku.fiIndustry
Shipbuilding
Location
Turku, Finland
Base material
AI, Fe, Ss
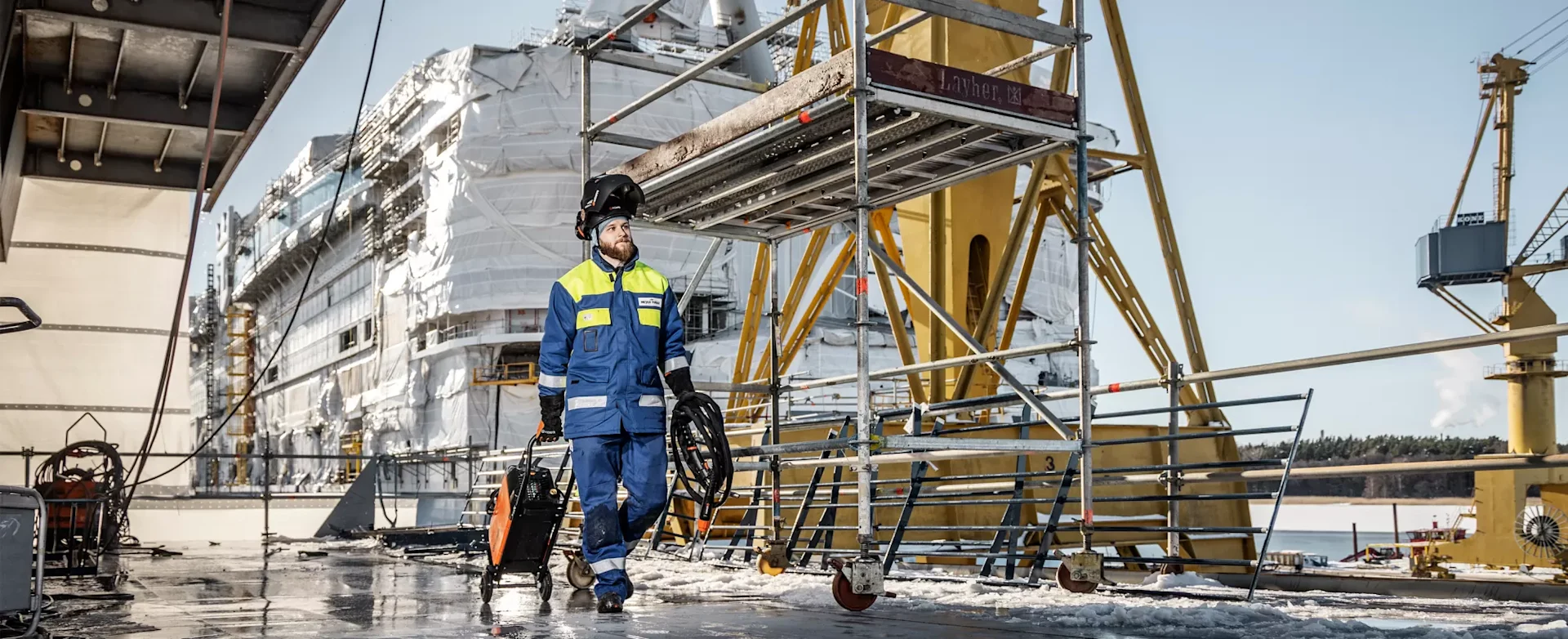
At shipyards, it is crucial that the welding machine is agile, mobile and lightweight.
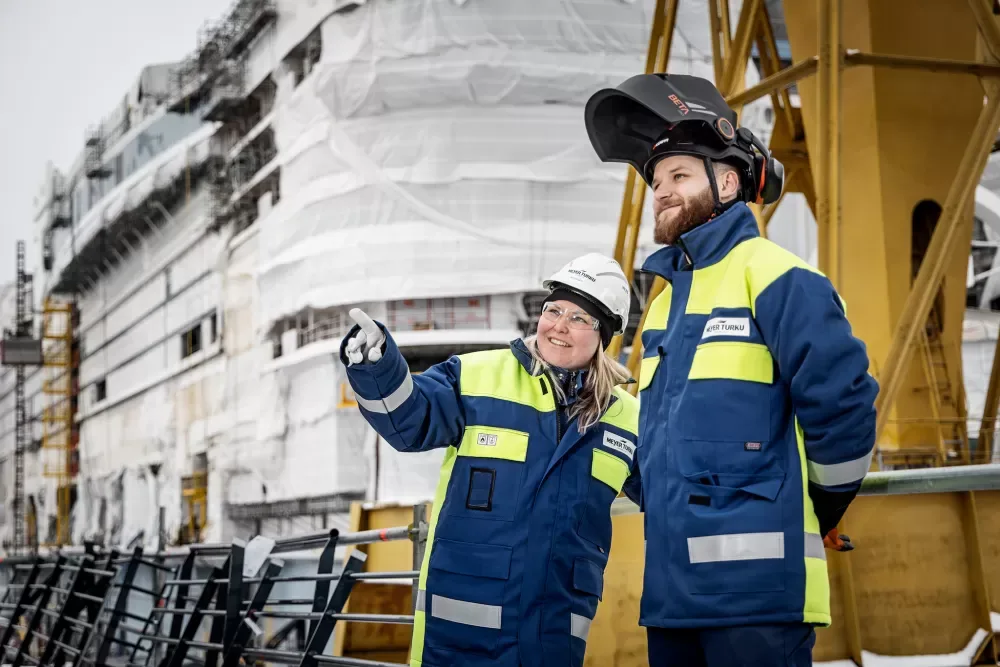
Sanna Nyholm and Miro Sarenko from Meyer Turku, Finland.
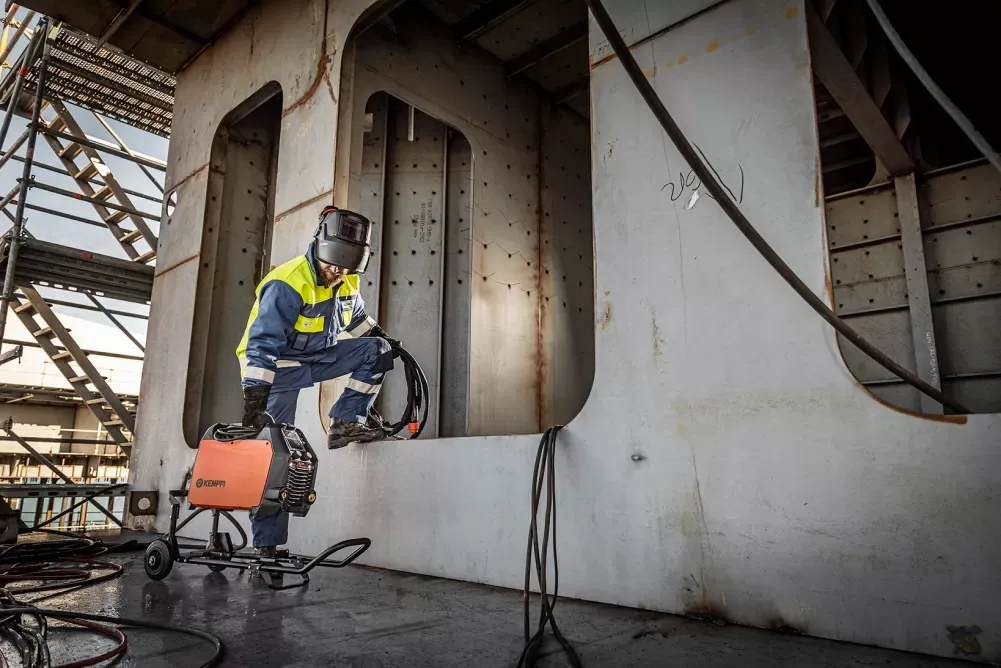
With Master M 323 you don't have to compromise on portability or power.
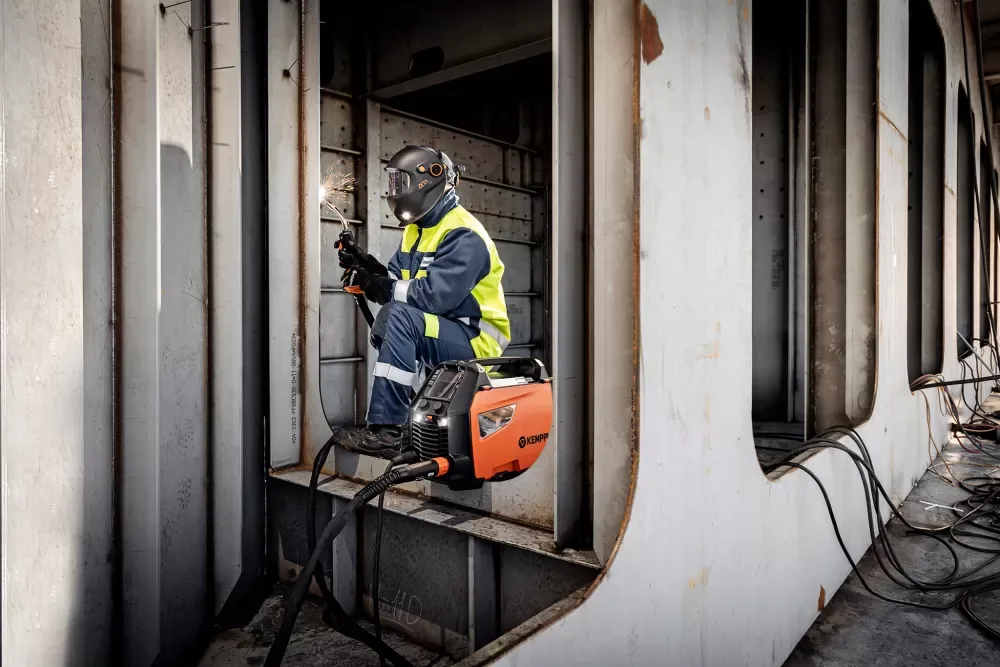
With Master M 323 you don't have to compromise on portability or power.
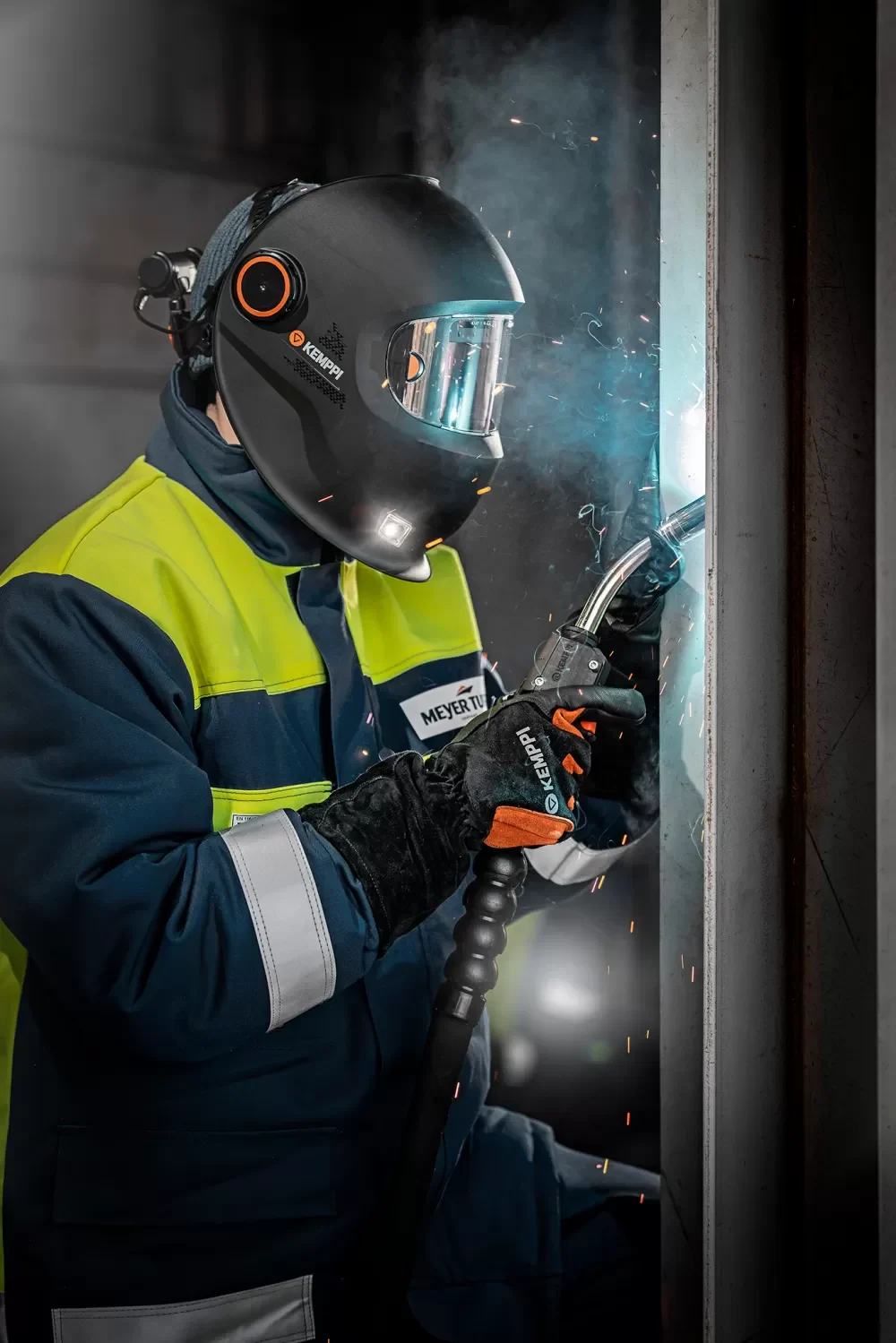
The power of 320 A is sufficient even for thicker materials to be welded, which increases the use cases for the Master M 323 considerably.
Featured Solutions
Product family
The Master M 205 and the Master M 323 set new standards for power and performance in a portable MIG welding machine. With a compact, lightweight design that's easy to carry, you'll enjoy having a portable MIG welder that can be moved wherever you need it.